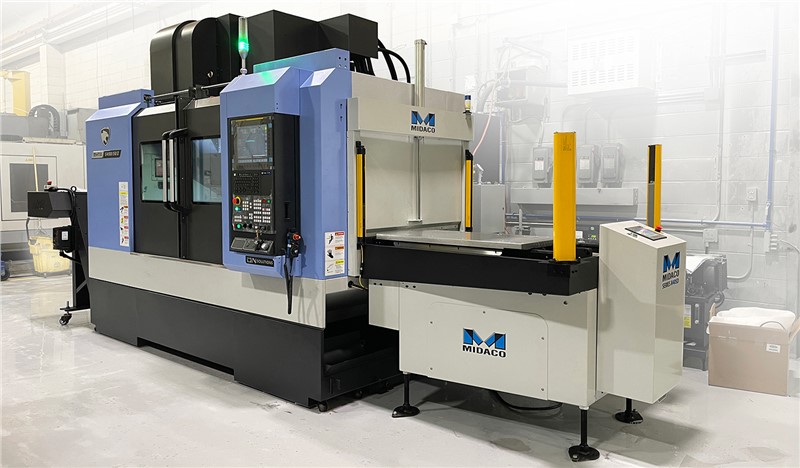
Making Vertical Machining Centers Into Metal-eating Rock Stars
Is your vertical machining center spending more time idle than making chips? If the spindle isn't cutting while you're loading parts inside the machine tool, you’re missing out on serious productivity gains.
🔹 Reduce Downtime – Keep your spindle running while setting up the next job.
🔹 Improve Ergonomics – No more reaching into the machine every cycle.
🔹 Automate High-Mix, Low-Volume Work – Yes, it does make sense!
Check out this article in Shop Metalworking Technology on how Midaco Pallet Changers can transform your machining process.
By Kip Hanson
If you’re the proud owner of a flexible manufacturing system (FMS) or manage a milling department filled with pallet pool-equipped horizontal machining centers, feel free to skip ahead. The same is true for those with the foresight — and sufficient budget — to invest in vertical machining centers that left the factory with integrated pallet changers installed. This article doesn’t apply to you.
Before you turn the page, however, congratulations are in order. Your shop enjoys much less downtime and far greater flexibility than does this story’s intended audience — the vast majority of machine shops that load their verticals as if they’re still operating a manual knee mill, making one part at a time.
“It doesn’t make chips.” That’s one of the more frequent criticisms aimed at Mike Munao when presenting his products to a prospective customer. The vice president of sales for MIDACO Corp., he’s used to comments like these, and counters them with an unfortunate truth. “When not equipped with some sort of pallet changing mechanism, vertical machining centers are the least productive machine tools in the shop.”
From Least to Most
This article isn’t a sales pitch for MIDACO or any of the others interviewed. It’s a fact of life. Whether you own a drill/tap machine, a gantry mill, or a three- or five-axis machining center, you’re shortchanging your overall equipment effectiveness (OEE) by not keeping the aforementioned doors closed as much as possible, the spindle happily whittling away at whatever workpieces sit clamped within.
Ergonomic Benefits
Wouldn’t all of this be easier and more repeatable outside the machine? And setting aside the operator’s aching back, what about the three to five minutes (or possibly more, for a fully loaded table) that the spindle sits idle every time the red light comes on? “These were the same problems that MIDACO faced when it first operated as a job shop more than five decades ago,” says Munao. “Like many shops, we became quite busy over time, but instead of buying another machine or starting a second shift, the owner’s son — Mike Cayley Jr. — designed our first pallet changer {the MPS-31 Micro Pallet Changer}.”
Credit: Full Article by Kip Hanson in Shop Metalworking Technology March 4, 2025
For more information on MIDACO Pallet Changers
Call or complete our online contact form today.
Comments