Spark R&D Reclaimed Hours of Machining Time by Adding MIDACO Pallet Changers
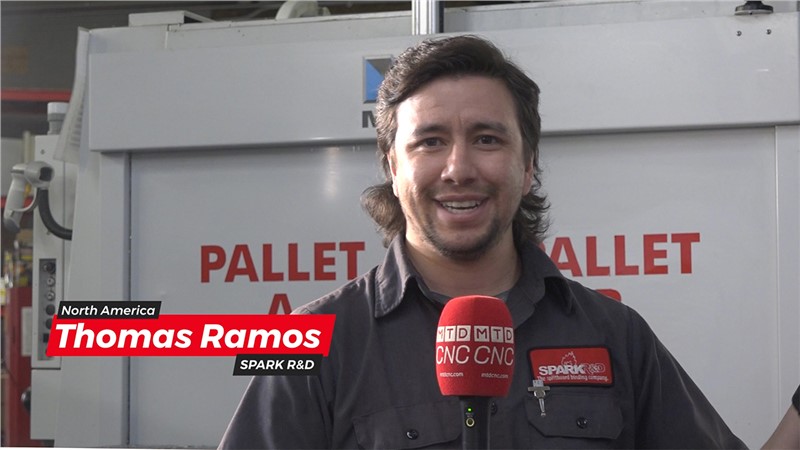
Spark R&D, located in Bozeman MT, knows first hand the productivity value and time saving gains
MIDACO Automatic Pallet Changers bring to shops that have multiple different part set-ups, which cause spindle idle time.
Spark R&D's Production Manager,
Thomas Ramos, says...
“It all comes down to - Is your spindle running?… When you own a bakery you don’t have ONE pan and wait for the bread to come out {of the oven} and then clean it, and put it back in and wait for it again… you have TWO pans. That’s what we’re doing here.”

Boosting Efficiency with MIDACO at Spark R&D - The Splitboard Binding
Company
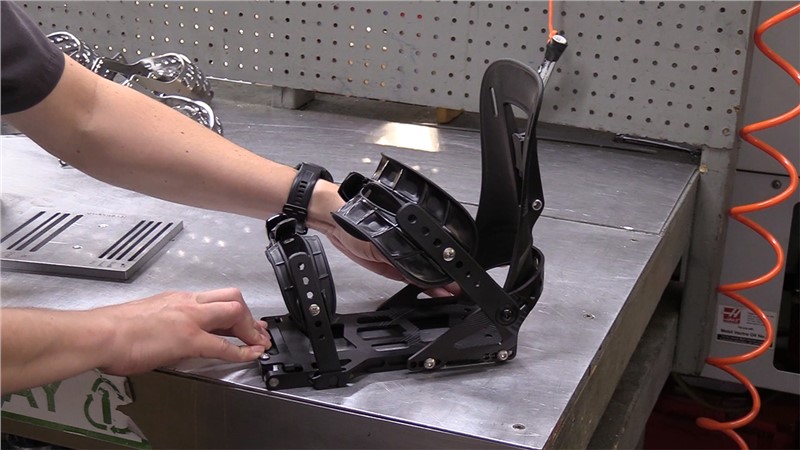
In the world of manufacturing, efficiency is the key to
success. Spark R&D - The Splitboard Binding Company has taken a
significant step in enhancing their productivity by implementing MIDACO Automatic Pallet Changers on their HAAS VMCs (Vertical Machining Center). This innovative solution has transformed their
operations and saved them valuable time in manufacturing their split board binders.
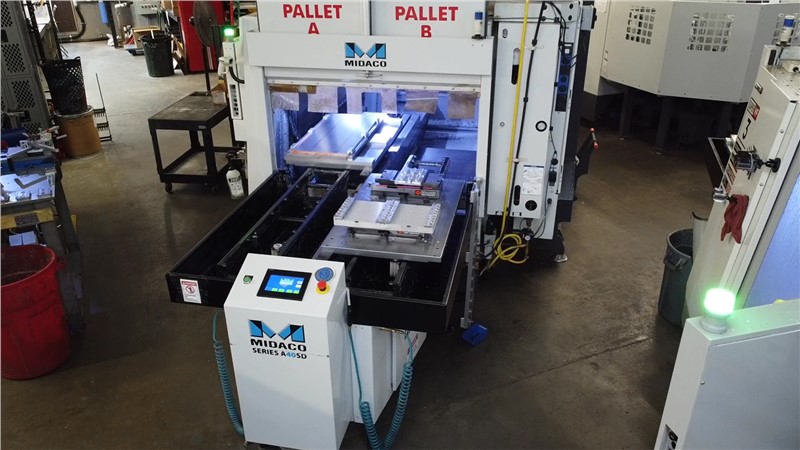
Maximize Efficiency Inside the Machine
One of the most significant challenges in any machining
process is the downtime caused by fixture setup. Before incorporating the
MIDACO pallet changer, Spark R&D faced hours of spindle
idle time due to the time-consuming process of setting up fixtures. However,
thanks to this smart automation solution, those idle hours have become a thing
of the past.
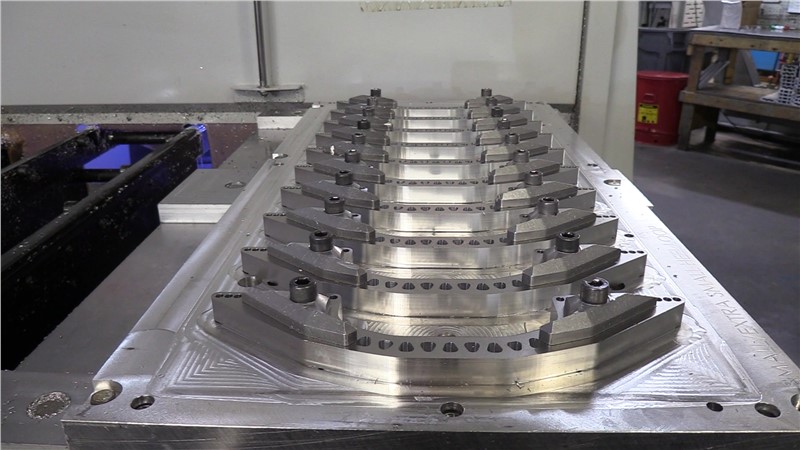
As Thomas states, "We've maximized the efficiency inside of the mills. The space that we have — the footprint inside of the mill to be able to be machined — we've maximized that to about what we can handle. We've done that by creating these massive fixtures. It makes our part cycle time longer, which in turn makes more parts... which is a great thing.
"However, making more parts creates more downtime when you're reloading those parts. We used to load 30-40 parts {with a 15 minute downtime}, now we're unloading 96 parts which leads to even more downtime within that 8 hour shift."
So what's the solution?
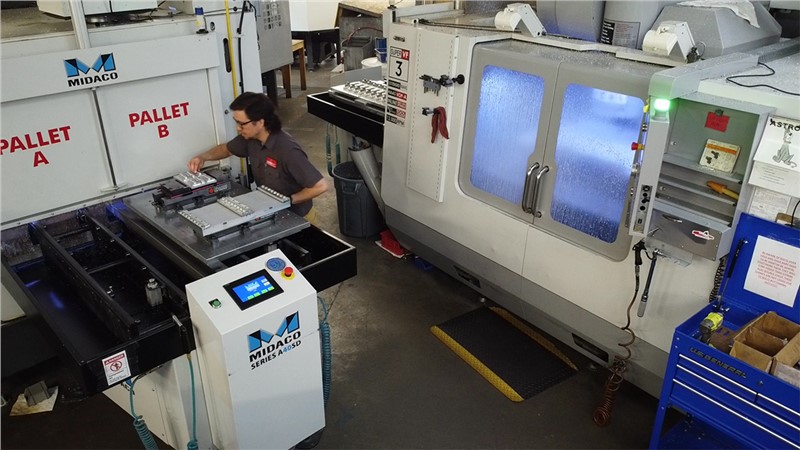
Hours of Fixturing Set-up Done Outside the Machine
Thomas describes the benefits Spark R&D has experienced with MIDACO pallet changers, "You have the set-up outside the machine to take off these massive fixtures that can weight 25 pounds each, which you have to lift in and out. If you do that outside of the machine, you're gaining spindle time and you're running while you're doing that... that's a HUGE benefit. 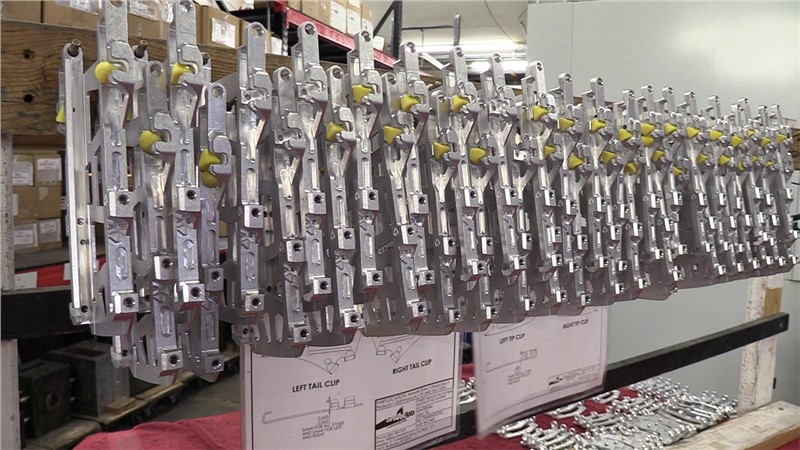
"We have 40-45 skews just on the vertical machines. We have to set up for these twice a week potentially. We have to run flat parts, we have to run 3D parts, things like that. Change overs are a real thing in this industry, so helping anywhere we can in that respect is huge. Cutting down in that {change over time} is very difficult without something like this {pallet changer}.
Is Your Spindle Running?
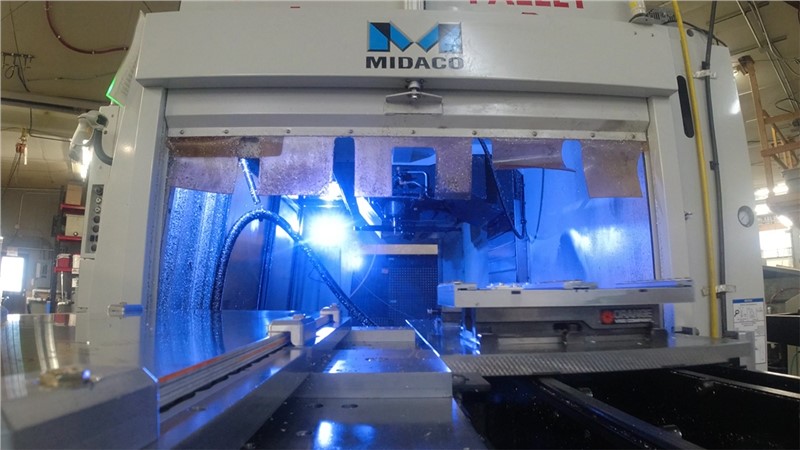
"You can go into fastening, ball locks, you know all of that technical stuff, but it really comes down to 'Is your spindle running? That's what we've tried to focus on here. Especially in a horizontally dominated machine shop, it's east to see that having two pallets is way better."
Optimizing Parallel Workflows
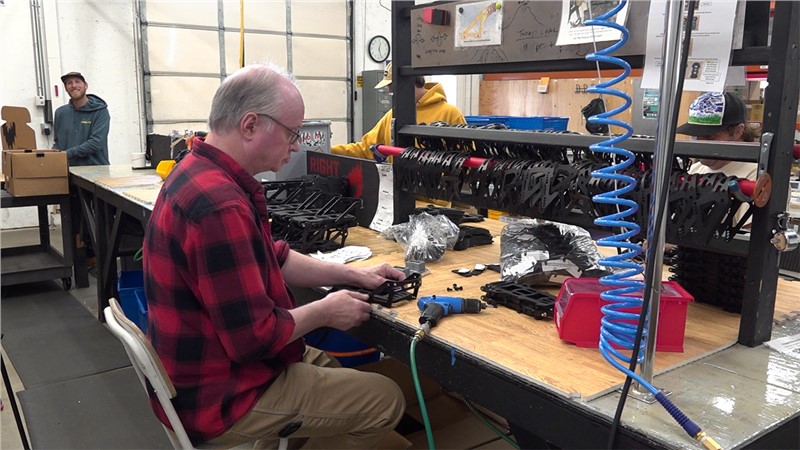
With the
MIDACO pallet changers in place, the company can
now set up fixtures and skew multiple parts outside the VMC while the machine
is cutting. This means that their HAAS VMCs can keep working continuously,
maximizing production output and minimizing any disruptions in the workflow.
"Automation has played a huge role in making the lives of our operators way easier... workflow — reloading — making things run as fast and as accurate as possible. With these {Haas} machines and now with the MIDACOs added on to them, it's a massive improvement that we've seen." - Thomas Ramos, Spark R&D
Key Benefits of MIDACO Pallet Changers:

1.
Reduced Downtime: By eliminating
fixture setup time, the company has significantly reduced spindle idle time,
leading to increased productivity.
2. Parallel Workflows: The ability to set
up fixtures and adjust parts while the VMC is in operation allows for a more
streamlined and efficient manufacturing process.
3. Enhanced Precision: The MIDACO pallet
changer ensures precise positioning, resulting in consistent and high-quality
machining with +/- 0.0001" (0.0025mm) repeatability.
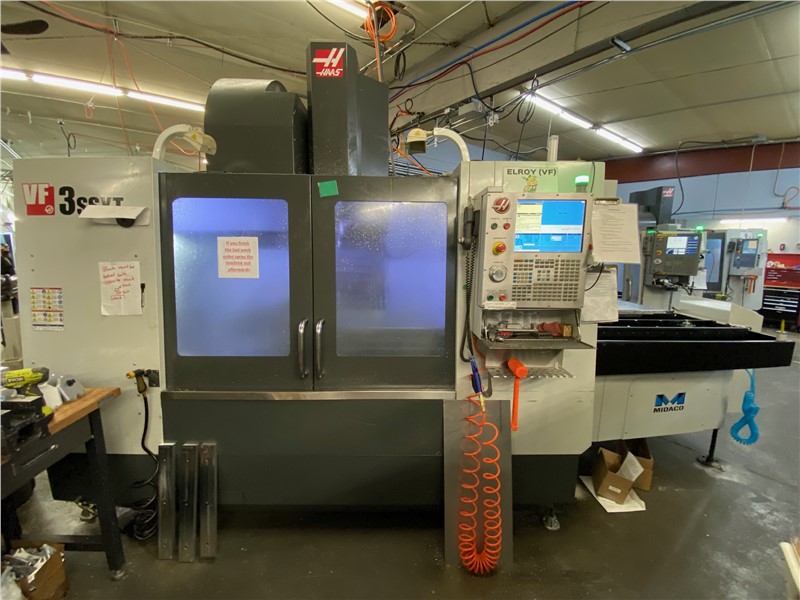
4.
Cost Savings: The reduction in idle
time and improved production capacity ultimately leads to cost savings, making
the investment in this technology highly worthwhile.
5. Profitability: If the spindle is running you're making more money. By eliminating an hour of spindle idle time per shift, Spark has reclaimed that lost time by running run 50-60 extra parts.
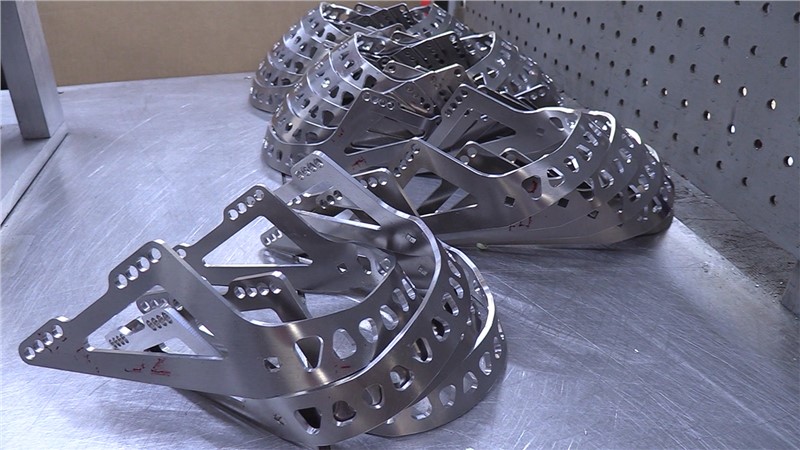
The story of
Spark R&D's success
with the MIDACO
Automatic Pallet Changers on their HAAS VMCs serves as a
testament to the transformative power of automation in the manufacturing
industry. By eliminating spindle idle time and optimizing their workflow, they
have not only improved their efficiency but also bolstered their
competitiveness in the market. This is a prime example of how innovation can
drive progress and prosperity in manufacturing.
For more information
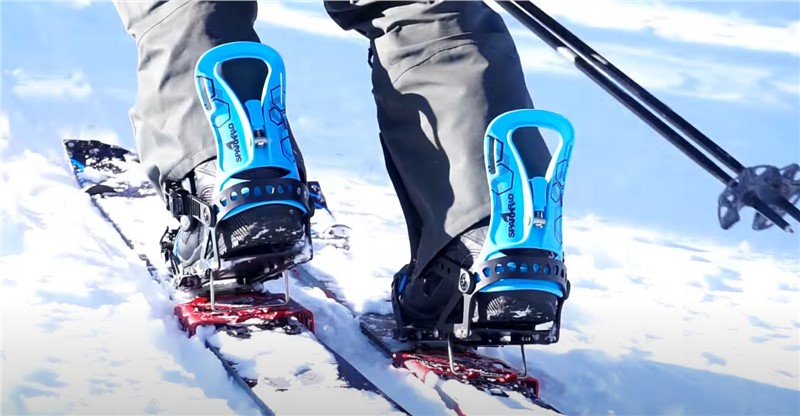
Video Credits:
Tony Gunn of MTD CNC North America
https://mtdcnc.com/#/North-America
Spark R&D - The Splitboard Binding Company
P.O. Box 3284
Bozeman, MT, 59772 USA
Ph: (866) 725 2085
www.sparkrndd.com
Facebook
Instagram
X (formerly Twitter)
YouTube
Comments